Dye (p. 41 )
1. Produced in Iwaizumimachi Shimoheigun, Hanaizumimachi Nishiiwai-gun, Morioka City, Iwate Prefecture.
2. Characteristics: Silk and cotton fabric dyed with Shikon, roots of Murasaki, Lithospermum erythrorhizon, and Akane Rubia akane. The color is mostly purple. There are 2 kinds: one is the Shibori(dapple) made of dyed cloth: the way is called Ato Zome, after dyeing, and the other Tsumugi, pongee, the fabric made of dyed threads called Sakizome, before-dyeing.
3. Uses: Kimono, sashes, bed linen and cushion cloths.
4. History: The origin is obscure but it has a history of 300 years, probably because good quality Shikon was obtained in this region. It has been a special product till the end of the Edo Period with the protection of the feudal government of Nanbu. Since the Kanbun Era(1789-1801) in the Edo Period, the Nanbu pongee was well known in Japan as it was an item to be dedicated to the Shogunate. Stripe patterns, after the era, came out after specialists were invited from Kyoto. Today, the tradition of cloth dyeing is maintained by the Fujita Family in Morioka City and that of thread dyeing by the Yaegashi Family in Iwaizumimachi. However, traditional Iwaizumi Nanbu pongee is not woven today because Fuji and Fuki Yaegashi, who are designated as "Intangible Cultural Properties", are very old. The Hanaizumi pongee is woven by Mr. Shimpei Onodera today.
Dyeing Method
The roots of Murasaki and Akane are used for the dye and the mordant is the lye of Nishigori tree.
1. Ato Zome, after-dyeing
Patterns, drawn on cloth with Aobana, sap taken from the flower of Murasaki Tsuyukusa, Tradescantia reflexa, are sewn with cotton threads. The cloth is dyed after the tie dye technique is applied with Nui maki or Take maki in which cotton threads or bamboo sheaths are used for tying. After the tied cloths are soaked in the dye, the threads are drawn out and the dyed cloth is steamed.
2. Saki Zome, Before dyeing
The stages of work are required to put the threads in the lye and to put them to dry in the sun. Then, the threads are put in the liquid, called Gojiru, obtained by grinding sodden soybeans. This process is repeated 3 times. Then the threads are kept for 1 year. After that, the dried threads are soaked 5 to 6 times in the dye and finally dried in the shade. Taumugi is woven by hand.
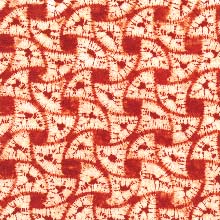
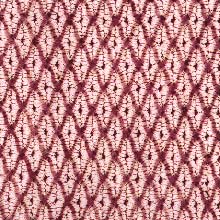
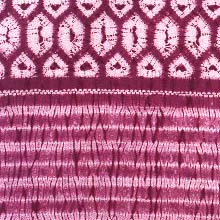
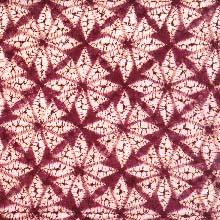